Achter de schermen ...
… bij het ABB Striebel & John project
Eén van de meest recente projecten waarin WEMO en AWL samen optrokken was het project voor ABB Striebel & John (S&J). We vroegen Jules van Hooijdonk (Projectleider bij WEMO), Harold van Pinxteren (Projectmanager bij WEMO) en René van de Meeberg (Projectmanager bij AWL) naar hun ervaringen met dit project en wat de kracht is van deze samensmelting tussen twee mooie Nederlandse machinebouwers.
Leestijd: 8 minuten
Wat is het eindproduct?
S&J is een toonaangevende fabrikant van energiedistributiesystemen. Zij produceren onder andere (schakel)kasten voor de huizenbouw. In Nederland maken we met name gebruik van een houten meterkast, maar in Duitsland zijn de meterkasten van staal en bevinden ze zich vaak in de gang of in de kelder. De behuizing van deze kasten wilde de klant, van coil tot aan eindproduct, in verschillende maatvoeringen volledig geautomatiseerd produceren.
Wat was de behoefte van de klant?
De kasten werden al gedeeltelijk geautomatiseerd geproduceerd, maar er kwam toch ook nog veel handwerk bij kijken. Daarbij was de huidige lijn aan vervanging toe. Ook was de afdeling Research & Development (R&D) bij S&J bezig met optimalisatie van de huidige producten en ontwikkeling van nieuwe types. Om kosten te verlagen, moesten ze verder automatiseren en moest de capaciteit wezenlijk omhoog. Hier zitten aan de voorkant enorme investeringen vast, die intern eerst goedgekeurd moesten worden.
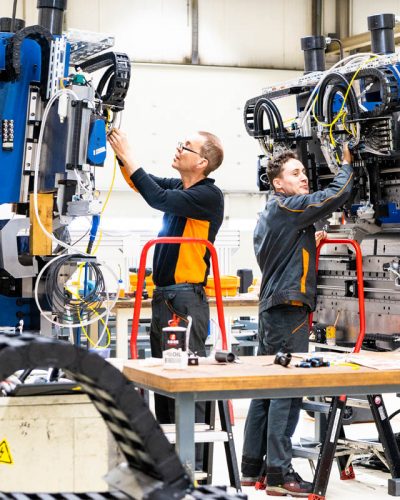
Welke afwegingen zijn gemaakt naar een passende oplossing voor S&J?
Een hoge automatiseringsgraad was de basis in combinatie met een minimaal vloeroppervlak dat beschikbaar was en scherpe eisen aan cyclus- en omsteltijden. Daarbij waren er ook een aantal scherpe deadlines. De nieuwe producten moesten op de beurs geïntroduceerd worden en de bestaande lijn moest in de kerstvakantie afgebroken worden om plaats te maken voor de nieuwe lijn.
In de oorspronkelijke vraag was MAG-lassen het uitgangspunt. Met de inzet van MAG-lassen is nabewerking en slijpen vaak nodig, met laserlassen niet. Wat zorgt voor een aanzienlijk sneller productieproces en dus lagere kosten per product.
René: “In het verleden waren de kasten door het lasproces niet voldoende afgedicht, er moest achteraf veel met de hand worden nabewerkt. Doordat wij met een laserlasoplossing kwamen, kon S&J de productiesnelheid verhogen en de handmatige nabewerkingen als slijpen en kitten weglaten. Dit bespaarde uiteindelijk veel kosten.”
Jules: “Laserlassen geeft een enorm nette las af die niet nabewerkt of geslepen hoeft te worden. Het onderdeel kan na het schoonmaken, meteen gelakt worden. Laserlassen stelt wel enorm scherpe eisen aan het uitgangsmateriaal. Om laserlassen als techniek toe te kunnen passen dient de lasspleet tussen de verschillende delen constant en heel klein te zijn. Hiervoor dienen de buigingen en ponsingen enorm nauwkeurig te zijn. Dat was de grootste uitdaging voor WEMO!“
Om laserlassen een succes te kunnen maken moet de klant aan de voorkant van het project de ruimte geven om mee te denken in optimalisaties in het product. S&J gaf die ruimte. Samen met de afdelingen Productie, Engineering en R&D van S&J, mochten WEMO en AWL meedenken aan een totaaloplossing, dit was voor alle partijen een enorm waardevolle samenwerking.
Één plus één is drie
René: “Wij wilden de klant helpen om de automatiseringsstap te maken. Als ervaren machinebouwer kunnen wij klanten helpen en hun productkennis aanvullen met onze automatiseringsoplossingen. Door dit samen op te pakken en samen op te trekken van het begin tot eind is het niet alleen een samenwerking, maar spreek je meer over een partnerschap.”
Harold: “We hebben de klant het vertrouwen gegeven dat we er alles aan doen om zover te komen, en we hebben dat vertrouwen teruggekregen.”
Samen met S&J zijn de machinebouwers gaan kijken naar de wensen bij de nieuwe producten en mochten ze diverse aanpassingen in het productontwerp doorvoeren. De maten en toleranties zijn uiteindelijk in de producttekeningen zo aangepast dat het product aan alle wensen van de klant voldoet en toch snel, betrouwbaar en nauwkeurig gemaakt kan worden. Het resultaat is dat er vanuit de oplossing van WEMO vier kastdelen met perfecte pasvorm aan AWL konden worden overgedragen zodat zij deze volledig geautomatiseerd verder konden verwerken. De oplossing die werd aangeboden door WEMO en AWL was van grote meerwaarde voor de klant. Dit is bereikt door anders te denken en door kennis en kunde te bundelen.
Jules: “De nauwkeurigheid hebben we bereikt door de gebruikte positioneermethode, waarbij we steeds dezelfde referentie hebben gebruikt. Zo werden de onnauwkeurigheden (toleranties) niet bij elkaar opgeteld en tolerantieopbouw voorkomen. Uiteindelijk hebben we de ponsgereedschappen middels praktijktesten geperfectioneerd tot een optimale vorm voor het uiteindelijke eindproduct.”
René: “Samen hebben we gekeken naar het productontwerp en het concept daarop aangepast. Als je het met de klant aan de voorkant al over het productontwerp kunt hebben, dan is één plus één, drie. Dit komt ten goede aan de kwaliteit van het eindproduct.”
Harold: “De mogelijkheid om in het product van de klant mee te denken om een zo optimaal mogelijke productielijn te kunnen ontwerpen is super waardevol voor S&J. En daar doen we het allemaal voor.”
Wat was de grootste uitdaging in het project?
Dat waren de productontwikkeling, de diversiteit aan producten en materiaal op een lijn en de snelheid. Daarbij waren de deadlines uitdagend, er moest een lijn geleverd worden waarvan de specificaties nog niet vastlagen. Het uiteindelijke productontwerp moest vastliggen voordat tot levering van de lijn kon worden overgaan. De producten van S&J moeten aan strenge normen en eisen voldoen, denk aan brand- en watertesten en het product moest visueel aantrekkelijk zijn.
Harold: “We waren constant afhankelijk van goedkeuring, van R&D van S&J, maar ook van AWL voor wat betreft de lasbaarheid. Dit vroeg om zeer scherpe en nauwe samenwerking.”
Het Coronavirus bracht een onverwachte dimensie in het project. Door de nieuwe machinelijn van S&J, konden zij ten opzichte van andere bedrijven wel (schakel)kasten leveren in deze tijden. Hierdoor kregen ze heel veel bestellingen binnen en moesten ze binnen no-time opschalen.
René: “Toen het Coronavirus uitbrak was de productielijn nog niet klaar en afgenomen. Uiteindelijk hebben we ons flexibel opgesteld en hebben we ervoor gezorgd dat de productielijn eerder draaide. Het vroeg ook om anders denken, zo hebben we een HoloLens ingezet om met de klant op locatie mee te kunnen kijken. De impact van het virus had niemand voorzien en het was zeker niet het meest ideale scenario, maar dankzij een goede afstemming onderling hebben we het tot een goed einde gebracht.”
Dankzij de flexibiliteit van alle partijen, kon S&J versneld produceren en inspelen op de marktbehoefte. Samen hebben we er alles aan gedaan om dit voor de klant te realiseren.
Wat is de kracht van de samenwerking tussen WEMO en AWL?
Door in een vroeg stadium een eenheid te vormen kun je processen goed op elkaar afstemmen. We zijn afhankelijk van elkaar. AWL heeft een goed product nodig en WEMO moet weten wat de vereisten zijn van dat goede product. Het is constant balanceren tussen de eisen van de klant, de wensen van AWL en de mogelijkheden van WEMO. Dit is essentieel om tot een goede oplossing te komen. Weten wat nodig is om het optimale voor de klant eruit te halen. Dan is het erg waardevol als je al eerder succesvol hebt samengewerkt.
René: “In een vroeg stadium moet je de juiste mensen van AWL koppelen aan de juiste mensen van WEMO. We hebben beide specialisten in huis die dezelfde taal spreken. Als die met elkaar praten, kan er veel en ontstaat er magie.”
Harold: “Ik weet dat S&J verwachtte dat twee Nederlandse machinebouwers nauw konden samenwerken. Tijdens het project heerste een snelle, directe communicatie en een zeer professionele en oplossingsgerichte manier van werken. Ook durfde we de klant in onze discussies mee te nemen. Dit zorgde ervoor dat we nooit de makkelijkste weg voor één van de partijen kozen, maar altijd bleven vechten om tot de beste oplossing voor alle partijen te komen. Het bleek niet altijd even makkelijk, maar uiteindelijk is de verwachting van de klant wel uitgekomen.”
Terugkijkend op het S&J-project. Waar zijn jullie het meest trots op?
René: “S&J heeft een oplossing staan die toekomstbestendig is. Met deze geautomatiseerde oplossing kunnen zij de komende jaren blijven produceren.”
Jules: “Het was een continu proces samen met de klant, WEMO en AWL. Dit red je alleen door er samen, vol vertrouwen, heel onbevangen en oplossingsgericht in te staan en je kijkt hoe ver je kan komen.”
Harold: “Wat ik zo gaaf vond, was de opdracht om samen met de R&D- en Productieafdeling van de klant en AWL een productrange te optimaliseren zodat deze geschikt was om volledig geautomatiseerd te produceren en daarbij de productiefaciliteiten te mogen leveren tegen een onwijs scherpe projectplanning. De onmogelijkheden van de opdracht hebben we één voor één weggepoetst en binnen de gestelde deadline een machine opgeleverd.”